Lean Manufacturing and Lean Management have been popular in the industry for years, supporting organizations in optimizing processes, eliminating waste, and increasing efficiency. A key element of both philosophies is lean manufacturing and lean management tools, which enable the implementation of these principles in practice. In this article, we will discuss the basic definitions, key methods, and specific tools that help companies implement Lean assumptions.
Lean Manufacturing – Definition And Assumptions
Lean Manufacturing – What Is It?
Lean Manufacturing is a manufacturing management concept that focuses on eliminating waste (muda), improving quality, and optimal use of resources. It was pioneered by the Toyota Production System (TPS) and introduces principles that help companies achieve better production results. For example, the use of Lean Manufacturing tools allows you to achieve shorter production lead times, better quality of manufactured products, lower costs, much better use of machines (which in traditional approaches are used only in 35-60%), reduction of downtime, and finally better organization of work.
Main Principles Of Lean Manufacturing
Lean Manufacturing is based on five key principles that create a coherent system that supports companies in delivering value while minimizing costs and waste. These include:
- Determining customer value – understanding which elements of the process are of the greatest value to the customer.
- Value stream mapping – process analysis to identify waste.
- Flow creation – streamlining processes to ensure continuity of work.
- Pull system – production on demand, reducing overproduction.
- Striving for excellence – continuous improvement of processes (Kaizen).
Why Is It Worth Using The Principles Of Lean Manufacturing And How Can They Contribute To Improving The Company's Operations?
The application of Lean Manufacturing principles brings numerous benefits. First, it enables the elimination of non-value-added operations, resulting in increased efficiency and reduced costs. Lean also helps to build a solid foundation for increased competitiveness in the market by improving product quality and increasing customer satisfaction. Additionally, through continuous improvement, organizations can quickly adapt to changing market conditions and customer expectations, which is crucial in today's dynamic business environment.
Indicators that are most often improved by applying Lean Manufacturing principles
- Increased productivity
- Increase in machine utilization as measured by OEE
- Reduction of inventory in the course of production
- Freeing up space for production
- Shortening the time of transition from raw material to finished product
- Reduction of changeover Times
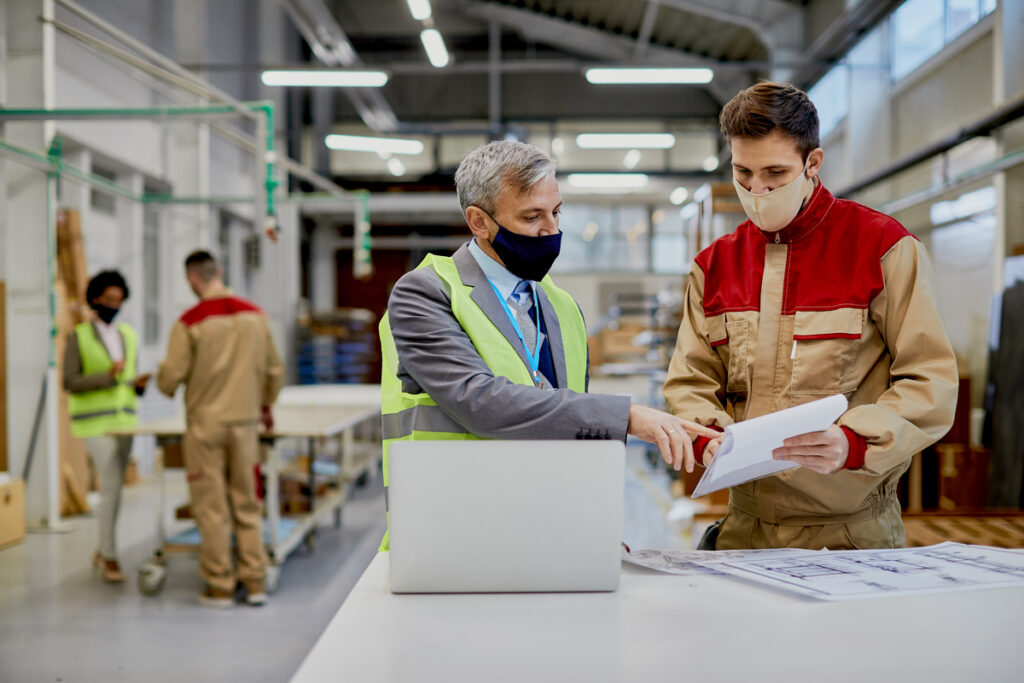
Lean Management – Definition And Application
Lean Management – What Is It?
Lean Management is a broader approach that includes management at the level of the entire organization. Its goal is to implement a culture of continuous improvement and effective resource management in every area of the company's operations, not only in production. Lean Management in practice means:
- Focus on eliminating losses in business and production processes
- Supporting teams in identifying and solving problems
- Leverage business process automation to increase efficiency
Applications of Lean Management in Business
Lean Management is widely used in various industries and areas of organizational activity, not limited only to the manufacturing industry. In production, it helps eliminate waste, optimize processes, and increase work efficiency. In logistics, it supports supply chain management through better planning, minimizing inventory, and reducing transportation times. In the services sector, Lean Management allows you to improve the quality of customer service by streamlining operational processes, eliminating unnecessary steps, and automating repetitive tasks. In administrative and office areas, it helps to standardize work, improve the flow of information, and minimize errors in documentation.
Thanks to its versatility, Lean Management is a tool that is used by both large corporations and small enterprises, allowing them to build a culture of continuous improvement and better management of resources.
When deciding to implement the concept of Lean Management, it is worth remembering to conduct a thorough analysis of processes in the company, identify problems, and train employees. Managing a company by the principles of Lean Management should be a continuous and comprehensive process, during which comprehensive changes will be systematically introduced regarding both the organizational structures and production processes.
Are you interested in Lean Management? See also the article dedicated to intralogistics: Lean Logistics: How does RTLS improve the implementation of lean management in intralogistics?
Main tools of Lean Manufacturing and Lean Management
In its assumptions, Lean focuses on the full use of resources and adapting the organization to the conditions that prevail in a given market. In order for the implementation of Lean Management to be effective, organizations have a number of tools at their disposal. Below we present the most important of them.
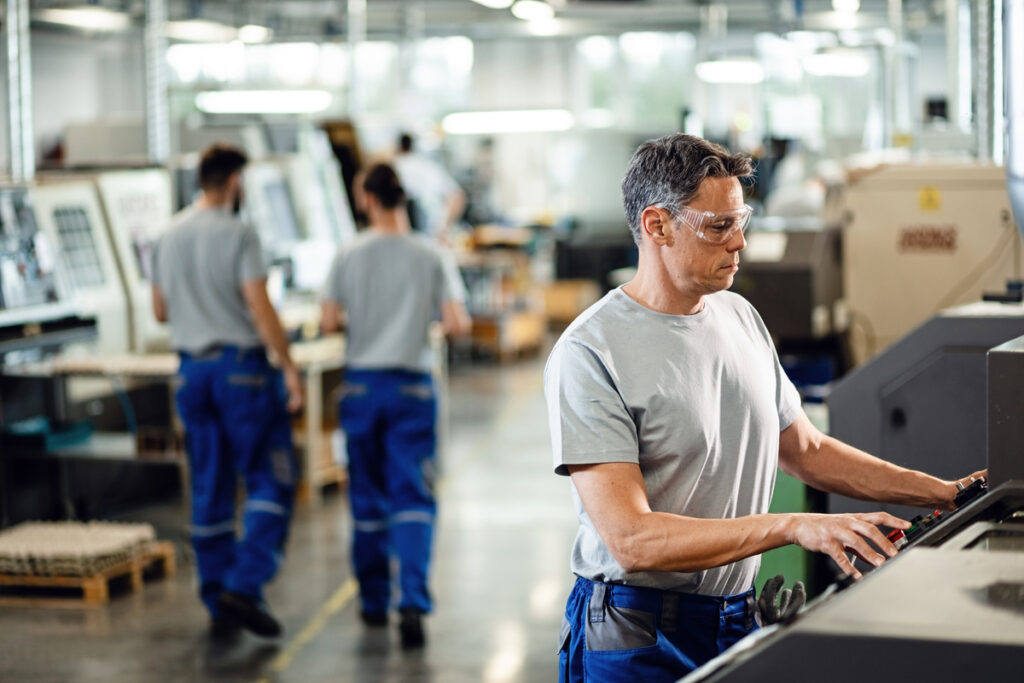
5S
One of the basic tools of Lean Management is the 5S technique, which is a set of rules that focuses on the organization and standardization of the workplace. Its goal is to create an orderly and secure production environment. The following 5S consists of the following stages:
- Sorting – elimination of unnecessary items.
- Systematics (Set in Order) – organizing tools and materials logically.
- Shine – keeping the workplace clean.
- Standardize – development of work standards.
- Self-Discipline (Sustain) – maintaining order and commitment in 5S.
Kaizen
Kaizen is a Japanese philosophy that means "continuous improvement". Kaizen assumes great involvement of employees at all levels, who, thanks to their ideas – even seemingly cosmetic ones – can have a significant impact on identifying problems and proposing improvements. The key benefits of using this approach are:
- Improving the efficiency of processes,
- Better quality of products and services,
- Increasing employee engagement.
Six Sigma
Six Sigma or Value Stream Mapping is a statistical method used in Lean Management 6 Sigma that helps to identify and eliminate the causes of errors in processes. It consists of the following steps (DMAIC):
- Define – understanding the problem and goals of the project
- Measure – collecting data and analyzing the current state
- Analyze – identification of the causes of problems
- Improve – implementation of solutions
- Control – monitoring and maintaining results
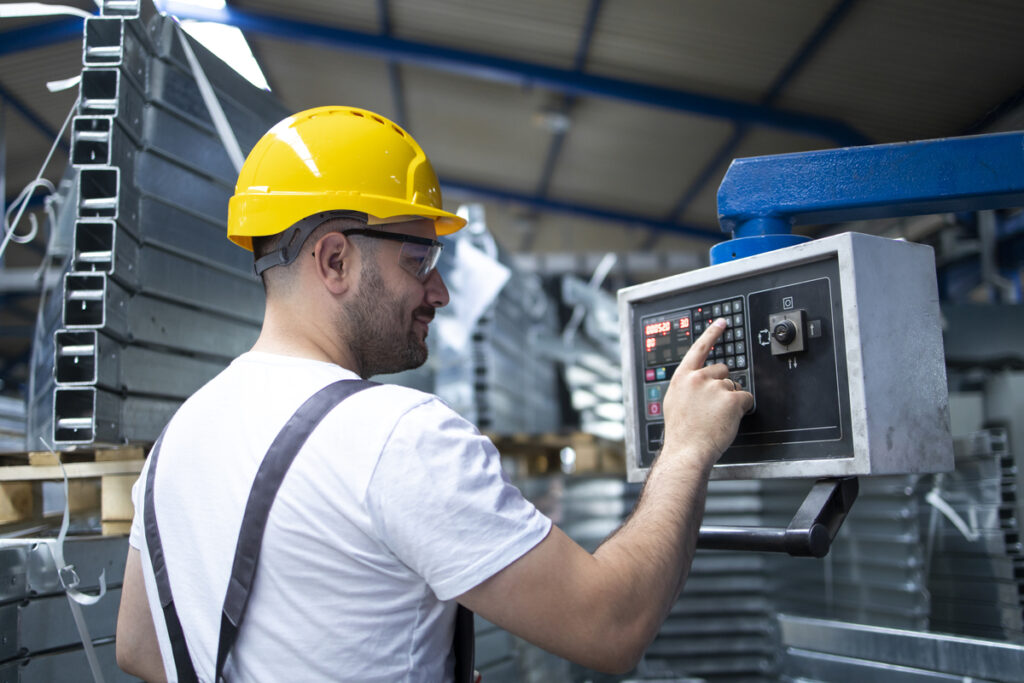
Total Productive Maintenance (TPM)
TPM is an approach focused on maximizing the availability of machines and equipment by preventing failures. The pillars of Total Productive Maintenance are:
- Preventive maintenance
- Self-service by operators
- Continuous improvement of equipment
SMED
Single Minute Exchange of Dies (SMED) is a technique that allows you to reduce the changeover time of machines. It allows companies to:
- Increase production flexibility
- Reduce downtime
- Reduce the costs associated with changeovers
Poka Yoke
Poka-Yoke is a method of error prevention that involves designing processes in such a way that it is impossible to make a mistake. Examples of using the Poka Yoke tool:
- Sensors to prevent incorrect installation
- Uniquely shaped connectors that fit only one way
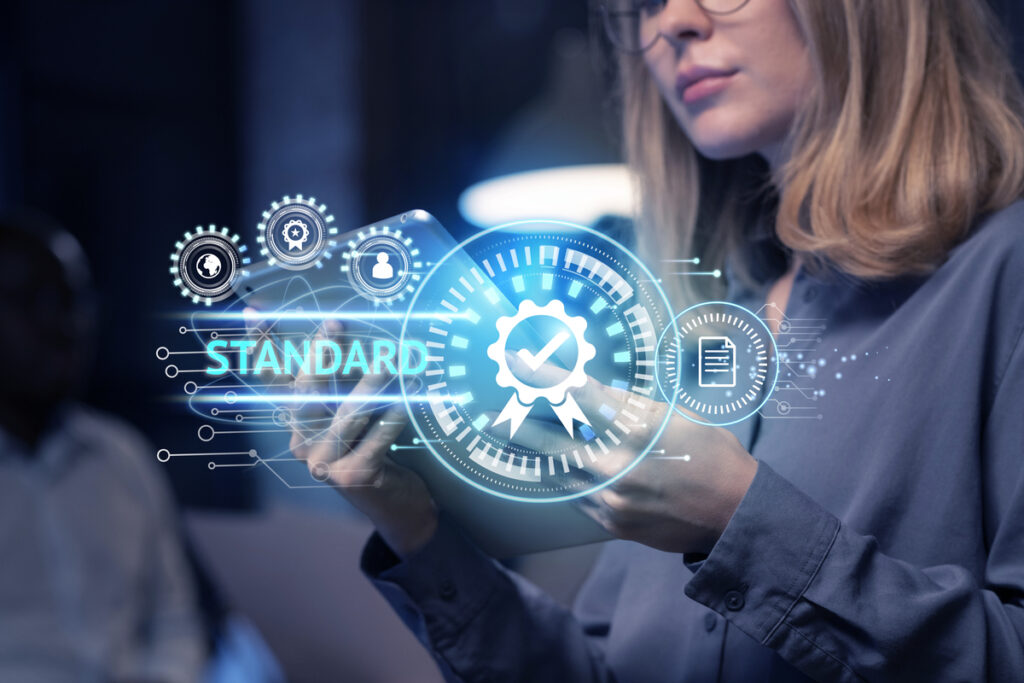
Standardized Work
Standardized work is a method of documenting best practices to ensure consistency and quality of processes. The elements of standardized work include:
- Specify the sequence of operations
- Standardization of cycle time
- Clear instructions for employees
Business Process Automation in Lean
Business process automation is a key element of Lean Management, supporting efficiency and eliminating errors. It enables organizations to:
- Increase the speed of task completion by automating routine activities
- Improve data quality by minimizing manual information entry
- Reduce operating costs by eliminating unnecessary processes
- Streamline workflows and eliminate bottlenecks
- Automation of routine activities,
By automating processes, companies can make better decisions based on more accurate analyses and forecasts. In addition, automation significantly reduces operating costs by eliminating redundant processes and reducing errors that could lead to costly rework or delays.
An example of the use of automation is the implementation of ERP software for production management. ERP (Enterprise Resource Planning) systems integrate various areas of a company's operations – from production, through procurement, to sales.
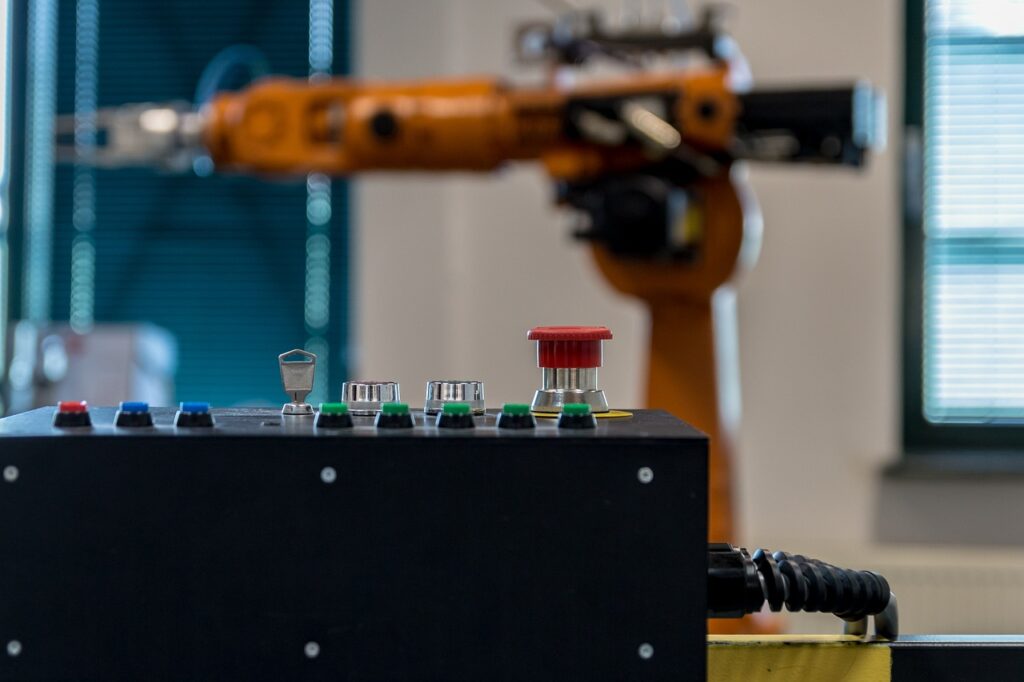
Another solution is Robotic Process Automation (RPA), which uses algorithms to perform repetitive tasks such as data entry or document analysis. With these technologies, companies can effectively manage processes, reduce the risk of errors, and increase the predictability of outcomes.
In production areas, automation supports the implementation of lean manufacturing principles such as Just-in-Time or Kanban, allowing for precise delivery of materials according to current demand. All this makes automation not only support Lean goals but also become an indispensable element of modern business transformation. In the long run, it leads to an increase in the competitiveness of the organization and an increase in its adaptability in a changing market environment.
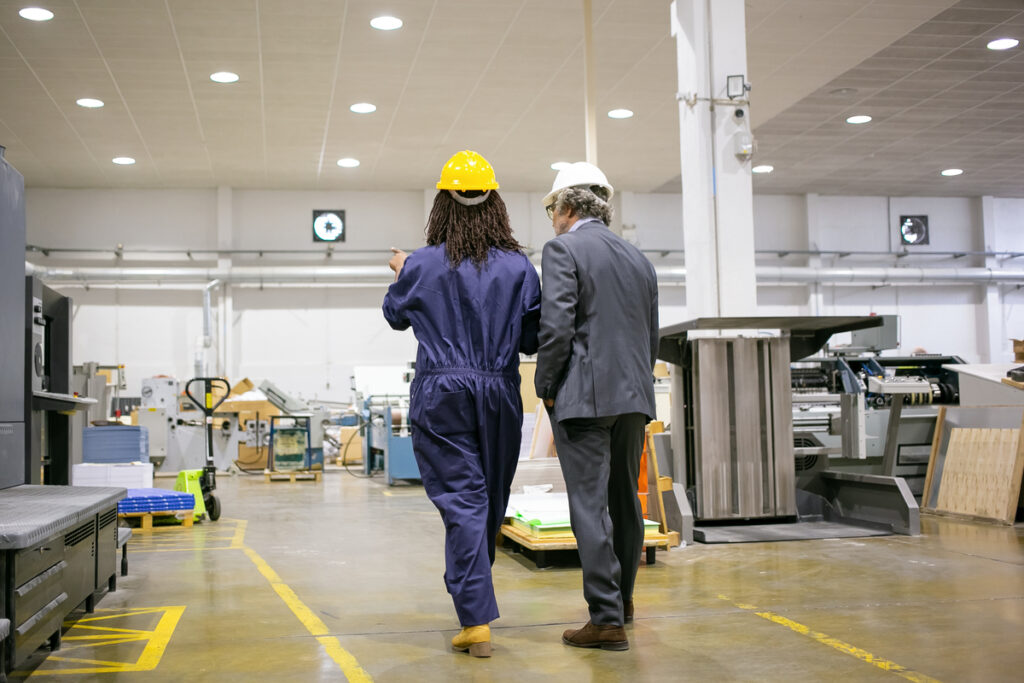
Summary – Why Is It Worth Implementing Lean Tools?
The implementation of Lean Manufacturing and Lean Management brings numerous benefits to companies. With techniques such as 5S, Kaizen, Six Sigma, TPM, SMED, Poka Yoke, and Standardized Work, organizations can not only achieve better results but also create a culture of continuous improvement. Let's remember that the main principles of Lean Management do not only come down to a set of tools, but it is also a lean culture, i.e. a management philosophy.
Lean Management is a concept that is not limited to production – its principles can be successfully applied in any area of business activity. Striving for excellence, eliminating waste, and team commitment are the pillars of success in today's fast-paced industrial world.
Want To Know More About Lean Manufacturing?
Check out our other articles on process optimization and the implementation of Lean Management tools in your company!