In the face of market challenges and growing cost pressure, companies are continuously looking for ways to increase efficiency. The logistics industry is particularly affected by this trend, and optimizing warehouse operations is crucial to staying competitive today.
In this context, the concept of Lean Logistics is gaining in importance, which becomes not so much an option as a necessity for entities wishing to achieve success. Lean focuses on eliminating waste and striving to increase efficiency in logistics, but in order to implement this philosophy fully and effectively, it is necessary to use advanced technological tools.
In this article, we will look at how RTLS (Real-Time Location Systems) technology can support Lean Logistics in warehouses and distribution centers.
Main Assumptions of Lean Logistics
Lean Logistics is a Japanese management philosophy focused on optimizing processes in the supply chain. Its primary goal is to deliver value to the customer at minimum cost and resources. In practice, this means analyzing every stage of the flow of goods, removing unnecessary operations, and maximizing the use of resources.
A set of Lean methods, originally developed in the automotive industry by Toyota, is also known as Lean Manufacturing. These methods were later adopted by many other industries around the world, becoming one of the most important approaches to production and operations management.
Lean Manufacturing is widely used today in industries such as manufacturing, logistics, services, healthcare, and even IT.
Lean Logistics - Key Benefits
The use of Lean Logistics methods allows organizations to achieve many significant benefits, which include:
- Eliminate waste - identify and remove all forms of inefficient management, such as unnecessary movements, downtime, or delays, to keep the warehouse as efficient as possible.
- Increasing efficiency - introducing processes that maximize the use of resources.
- Maximizing customer value - focusing on customer needs and adapting processes to their expectations.
The Biggest Challenges for Lean Management in Intralogistics
Implementing lean management in logistics is not an easy task. Traditional intralogistics, based on manual management of warehouse operations, faces many problems, such as:
- Lack of precise asset tracking, which leads to unnecessary delays, increases operational costs and contributes to errors.
- Suboptimal use of space, resulting in higher storage costs.
- The complexity of internal processes such as moving goods, loading, and unloading, generate excessive waiting times.
The answer to these challenges is the automation of warehouse processes supported by RTLS systems, such as efectivo.
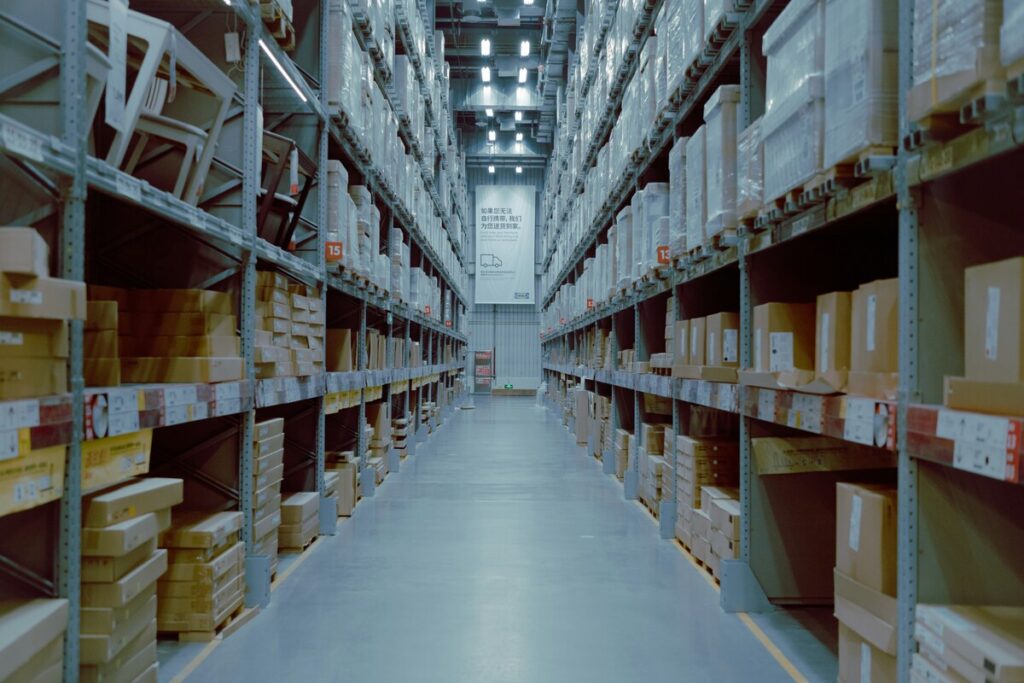
RTLS Systems in Intralogistics
In the area of intralogistics, where resource flow management plays a major role, RTLS (Real-Time Location System) technology is an indispensable element supporting the lean philosophy. Thanks to them, warehouses, where there is chaos, delays, and mistakes regularly, occur, have a chance to gain a "new life".
RTLS: What is it and how does it work?
RTLS (Real-Time Location Systems) is a technology that enables the precise location of assets in real-time. In intralogistics, RTLS can be used to monitor the movement of vehicles, employees, equipment, or goods in the warehouse. RTLS systems use various technologies such as RFID, Wi-Fi, Bluetooth, and UWB (Ultra-Wideband) to determine the exact position of objects.
Business Process Automation with RTLS
How does business process automation work? The idea is very simple – implementing such a solution means replacing repetitive manual activities with maintenance-free, self-acting ones. Automation of warehouse processes is therefore an important element of lean manufacturing, necessary for organizations that want to increase their competitiveness and improve the quality of services.
Business Process Automation (BPA), i.e. the use of technology and IT tools to automate, streamline, and optimize various operations, allows you to significantly increase the efficiency of the company's operations, reduce costs, and minimize the risk of human error.
What actions will RTLS automate?
The use of the RTLS system in the warehouse allows you to automate areas such as:
- Assign tasks to employees- RTLS systems can automatically assign tasks to employees based on their current location. This minimizes the time that employees move aimlessly around the warehouse.
- Warehouse fleet management – RTLS monitors the location of forklifts and other vehicles to better manage your fleet, optimize routes, and reduce fuel consumption.
- Asset tracking – The system allows for automatic tracking of people and vehicles in real-time, resulting in significant time savings and increased safety.
In addition, thanks to the integration of RTLS with WMS (Warehouse Management System) systems and other IT solutions dedicated to the logistics industry, it is possible to precisely manage virtually every aspect of work in the warehouse and increase efficiency.
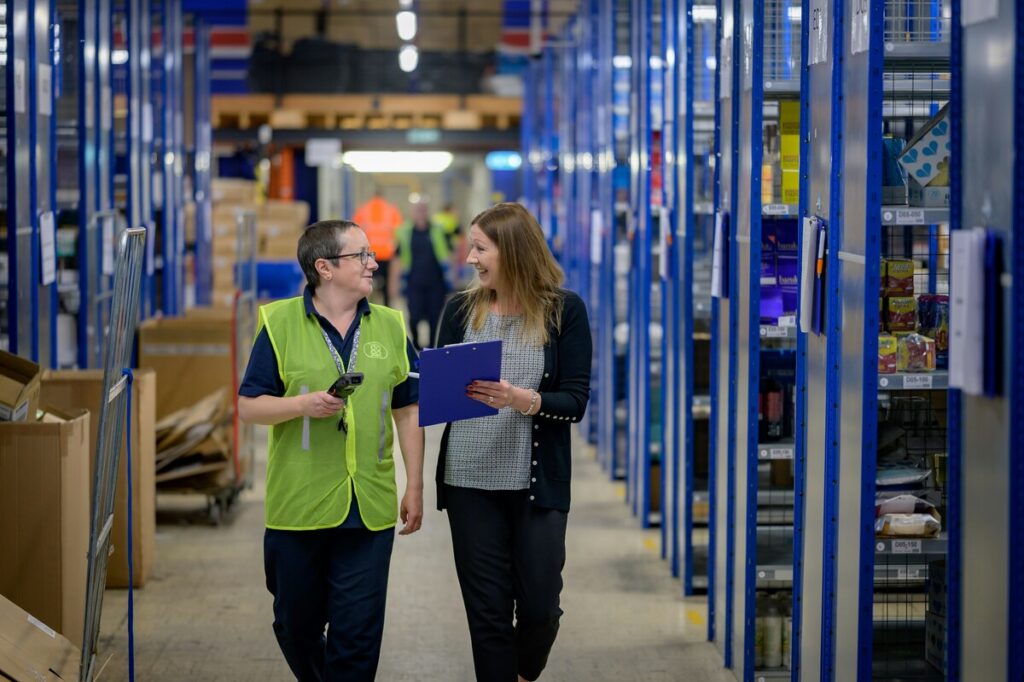
How does RTLS support lean management in logistics by optimizing business processes?
The implementation of an RTLS system in intralogistics brings many benefits that perfectly fit into the principles of Lean management. Here are some examples of how RTLS efectivo improves warehouse management in the spirit of Lean:
Asset tracking – RTLS efectivo enables precise monitoring of the location of people and vehicles at every stage of the warehousing process. This allows you to react quickly to inefficiencies, shorten order processing times, and reduce inventory costs.
Route optimization – Analyzing data from RTLS allows you to optimize the movement routes of employees and vehicles, such as forklifts, which improves work and reduces the time it takes to complete tasks.
Workforce management – efectivo technology allows you to track the movement of employees in the warehouse, which allows for better task planning. Optimizing processes in these areas relieves them of unnecessary activities and allows them to focus on the tasks that really matter.
Optimize storage space – With precise data on the location of resources, you can better manage available storage space, minimizing voids and streamlining rack layout.
Reduce downtime – Monitoring the flow of goods and resources eliminates bottlenecks, resulting in reduced waiting times.
Continuous Process Improvement – RTLS provides data that is analyzed to identify areas for improvement. In this context, it allows for continuous optimization based on up-to-date data from detailed data.
Standardization of processes — 5S supports the standardization of work in the warehouse, which, combined with RTLS monitoring, gives better control over space and material flow.
Process automation – automation of warehouse processes using RTLS allows you to reduce the working time of employees, who no longer have to look for vehicles, for example, as well as to optimize transport routes in the warehouse, which speeds up loading and unloading.
Decisions based on data analysis – the analysis of data collected by the efectivo system allows for a better understanding of intralogistics processes, better forecasting and adjustment of inventory levels, optimization of human work, measurement of efficiency, or identification of areas for improvement.
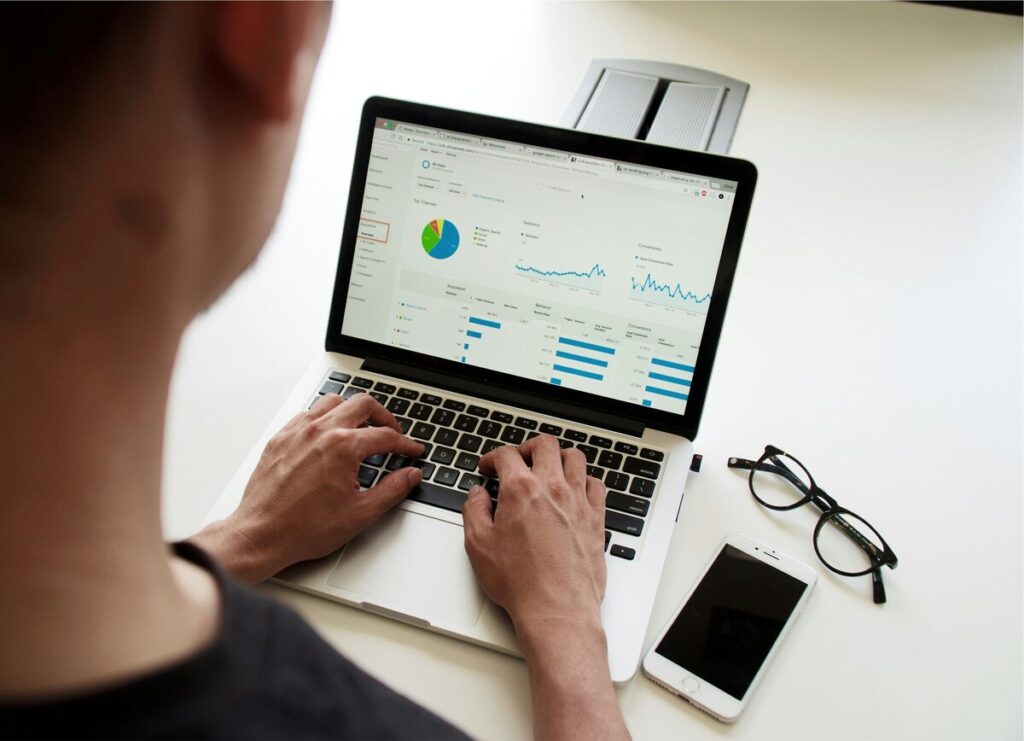
RTLS and selected Lean Logistics methods
Lean Logistics is based on the use of methods that help managers implement and improve the efficiency of logistics processes and directly affect operating costs and working time. The most popular methods are 5S, Kaizen, Total Productive Maintenance (TPM), Six Sigma, SMED, Standardized Work, Visual Management, Poka Yoke, and Training Within Industry (TWI).
Let's take a look at how RTLS technology and business process automation support selected Lean methods.
5S and RTLS
5S (sorting, systematics, cleaning, standardization, self-discipline) is a method that focuses on the organization of the workplace. RTLS can support 5S by, for example:
- Sorting: RTLS helps in identifying and removing unnecessary items from the warehouse.
- Cleaning: RTLS can help you identify equipment that has not undergone scheduled maintenance.
- Self-discipline: Assigning tasks to employees based on RTLS reports and measuring their completion helps to maintain high standards.
Kaizen & OEM
Kaizen is a philosophy of continuous improvement. RTLS supports Kaizen by:
- Real-time monitoring of processes allows you to quickly detect problems.
- Measuring selected parameters thanks to the ability to generate detailed reports. Data from the RTLS system can be analyzed to identify areas for improvement.
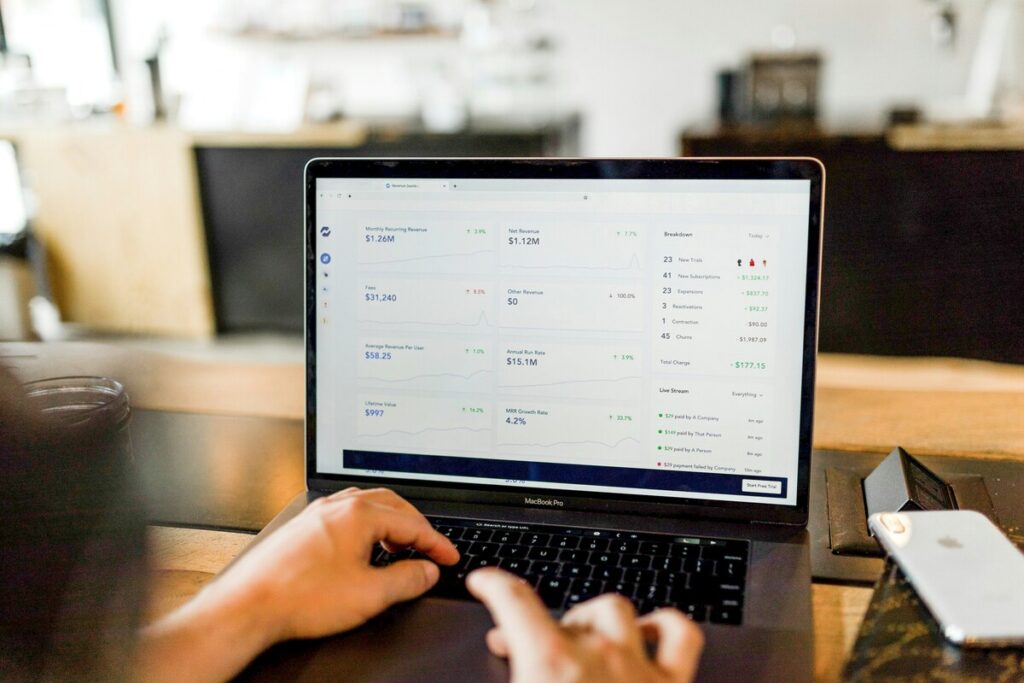
Total Productive Maintenance (TPM) and RTLS
TPM focuses on keeping machines and equipment in full productivity. RTLS supports TPM by:
- Equipment Health Monitoring: RTLS allows you to track the status and location of your equipment, making it easier to maintain.
- Maintenance planning: Data from RTLS can be used to plan equipment inspection and maintenance.
- Improving the safety of forklift trucks by introducing collision prediction algorithms.
Six Sigma and RTLS
Six Sigma is a quality management methodology that focuses on reducing defects and achieving perfection. RTLS can support Six Sigma by, among other things:
- Data collection: RTLS provides accurate data on processes, which makes it easy to analyze and identify problems.
- Process monitoring: This allows you to quickly detect and eliminate defects, e.g. analyze and document the actual flow of materials and employees, in order to identify inefficient routes (spaghetti diagram).
- Implementation of improvements: RTLS allows you to measure the effects of implemented improvements. For example, the Heat map report allows you to identify high-traffic areas and assess space usage.
SMED in RTLS
SMED is a method of reducing the set-up times of machines, devices, and processes. Here's how RTLS supports SMED:
- Optimization of changeover processes – thanks to reports such as the Spaghetti diagram, we can document and analyze the flow of resources in order to design assistance systems, for example, mobile workstations or better tool placement.
- Reduce downtime: Quickly detect and eliminate problems to reduce downtime.
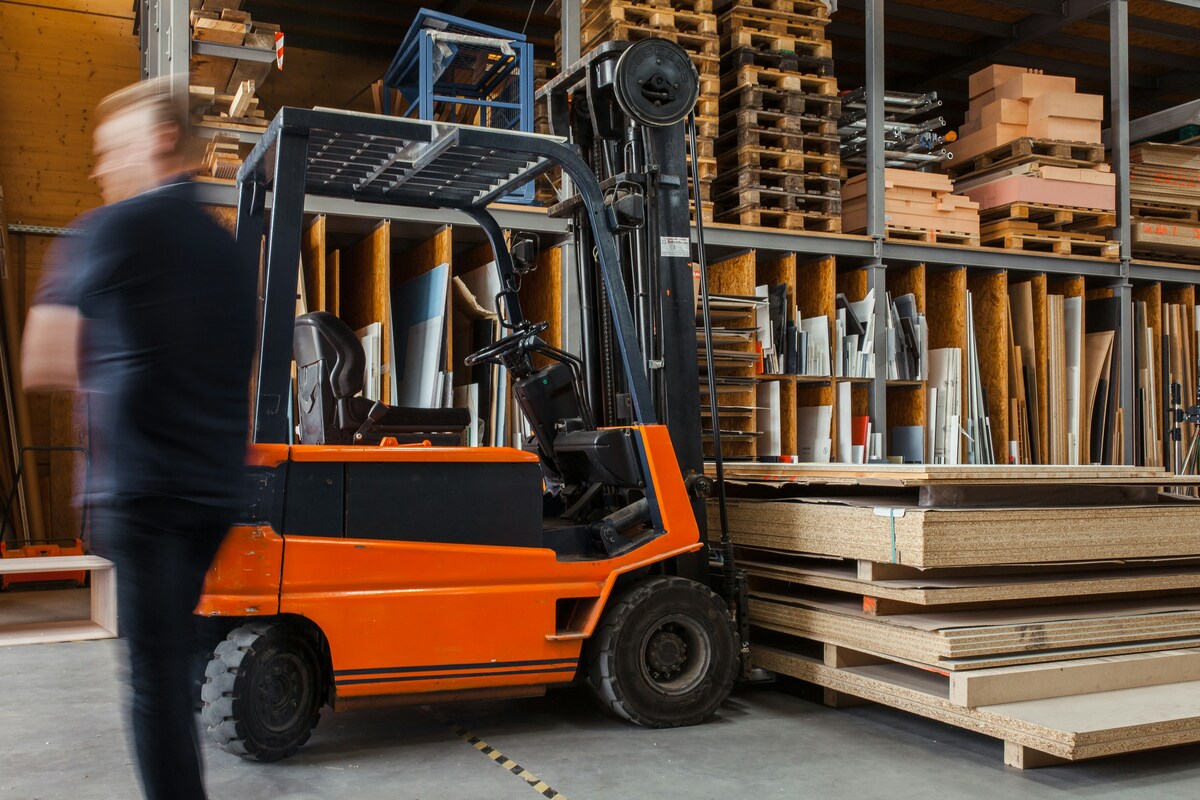
Summary
Thanks to Lean Logistics and process automation, companies can not only reduce their losses but also increase the quality of their services. In the era of rapid market changes, investment in technologies such as RTLS is becoming an indispensable part of any company's growth strategy.
Implementing RTLS in intralogistics is a key step towards improving operational efficiency. This technology has the potential to revolutionize logistics and fits perfectly into the principles of Lean Management. By accurately tracking assets, goods, and employees, businesses can achieve more efficient workflows, increase efficiency, and reduce waste. As a result, Lean Logistics with process automation is becoming a key tool in developing competitiveness and achieving success in the market.